Day One Monday, August 15th
Orientation
Twenty educators
gathered at Wanuskewin Heritage Park on Monday as a group of people with very
few connections. We knew there were common science education interests,
but that was about it. After introductions and an “express lane” review
of the plans for the week, Kate, Pam, and Brad very quickly immersed us into
the world of geology with a crash course on geological history and a review of
rocks and minerals. The looks on many faces were, “Oh yeah, I remember
that!”, while there were some who were pretty knowledgeable in the area.
The beauty of having so many educators together is we all started to learn with
and from each other.
We were
provided all kinds of information and resources from the SMA folks, including
lesson plans where someone has taken the time to make the connections to the
Saskatchewan Learning Outcomes and Indicators from grade 4 through high school
(we love those people!). We even got to participate in a rocks and
minerals identification lesson. Everyone got into it and I’m guessing
that lesson will certainly be repeated throughout the province, especially
because we were provided with a kit that contained the samples and equipment
that are required to teach it.
The group
was given an overview of the mining industry in Saskatchewan where we quickly
realized that Saskatchewan is a leader in the Canadian and international mining
industry. They are also world leaders in safety standards… and they’re
serious about that aspect!
The evening was
capped off by a dinner featuring bison and the opportunity to rub shoulders
with some of the industry and SMA leaders. They are passionate about what
they do, and they should be because the mining industry is pretty important in
our province.
By the end
of day one, we weren’t just educators who had a common interest… we started to
gel as a group of learners anxious to get to know each other better and to
embark on an experience of a lifetime. Can’t wait to get going on
tomorrow’s tour!
Terry Kikcio
Saskatoon Tribal Council
Education Unit
Day Two Tuesday, August
16th
PotashCorp Presentation
Today we began our day by jumping right in with both feet
and learning about potash and potash mining over breakfast! We started out with
an activity that can be used to teach students about how potash can be mined by
solution mining. SMA has created several lesson plans relating to the Potash
Kit that we used today - which I personally have used with my grade 7 students
in previous years - but even then I still learned some new activities this
morning that I will be able to bring back to my classroom to flesh out my
lessons and expand on my teaching of solution mining! For example, we learned
not only how the sylvinite ore can be dissolved and filtered to remove the
insoluble clay and iron oxide, but also that if you cool a supersaturated
solution of KCL and NaCl, that KCl will precipitate out of solution a lot more
effectively than NaCl will, meaning that you have an efficient method of
separating the two kinds of salts. This is especially useful in a place like
Saskatchewan, where you conveniently have this wonderful thing called winter to cool down the solution for
you! No extra energy required!
After breakfast and our hands-on solution mining activity,
we had a presentation by Angus Errington from PotashCorp giving us a bit of an introduction
to potash and conventional underground potash mining. We learned that potash is
made of four main components – clays, iron oxide, table salt (NaCl), and
potassium salt (KCl) – and we learned about why there is so much potash in the
middle of a place that is really far from any ocean. Potash is a result of an
inland sea that used to cover Saskatchewan a very long time ago, before North
American looks like it does today. He also explained how potash exploration
works, what makes a good location for a mine, some of the major geological
issues in the area, and where several of the potash mines in Saskatchewan are.
It was really interesting to learn about some geological
complications experienced by many who mine in Saskatchewan such as the water-bearing
Blairmore formation, and the unique problems of mining in a “soft rock”. In
order for a mine to sink a shaft through the Blairmore formation, the ground
needs to be frozen and reinforced while it is still frozen. You would typically
think that it is hotter underground the further down you get, but that is not
the case if you are trying to dig past a frozen, water-bearing rock formation!
However, I don’t think there could be anything scarier then knowing that the
rock you are mining through has a habit of bowing under pressure, both on the
ceiling and on the ground! Companies had to develop a special method of mining
to relieve the stress on the rock caused during mining, and they are designed
to fail after the miners have already
extracted what they needed and moved on.
After the presentation, it was time to get on the road and
head out to our first mine! Patience Lake, here we come!
Danielle Blackstock
The history of Patience Lake and its ability to adapt and
succeed under difficult circumstances was very interesting. It is the oldest mine in Saskatchewan. Rebuilding after one flood then deciding to restructure
after the second flood has resulted in Patience Lake being a unique example of
a solution mine developed from an underground shaft mine. They continue to stress the importance of
continued exploration in mining methods, processing and environmental
reclamation. Being able to see the
holding ponds, the dredge and the tailings pond was important to our
understanding of their unique situation.
Another
interesting part of this tour was the geology of the area. They often referred to Mother Nature’s role
in preventing seepage and minimizing percolation. The beauty of our cold
Saskatchewan winters allows the crystals to form naturally. Thus the mine is most productive during the
winter months. The tour guide introduced
us to the idea of overlaying the map of a familiar area with the map of the
mining area to give us some perspective on the size of mine sites above and
below ground. It was an excellent
reference for size and has continued to be an example we refer back to as we
continue our tour.
Potash Pete welcomes all,
In his red and blue standing so tall.
“Come in, come in, there’s lots to do.
The Interpretive Centre is the place for you!”
John and Richard beckon, “Welcome, everyone!”
Their enthusiasm is second to none.
In 1856 potash was found,
In Germany, 10,000 ft underground.
The word “potash” John said with a smirk,
Was actually plant ashes spread on the dirt.
First plants were burned, quite a lot.
Then the ashes boiled in a pot.
PotashCorp Patience Lake Mine
Patience Lake was the first official mine stop of our
Geoventure. We were immediately struck
by the pride each of our presenters had for the mining industry, their company
and their accomplishments as a company.
Their success as Emergency Response/Mine Rescue Skills Competitors was
proudly displayed and the importance of these skills was evident in each part
of the tour. They also stressed that
they were able to use their in-house trades people for maintenance, repair and
construction. It was all a part of an
environment of family and personal investment in the mine site.


I was also struck by the relevance of the Patience Lake
mining process to the Grade 7 Science units on Mixtures and Solutions and
Fluids as well as the examples that could be used in the Grade 8 Water Systems
unit. The information we are gathering
and the importance of the mining industry will certainly be rocking our
classrooms in many curriculum areas!
Patricia Ann McKay
& Trent Rumple
Potash Interpretive Centre – A Poem
Potash Pete welcomes all,
In his red and blue standing so tall.
“Come in, come in, there’s lots to do.
The Interpretive Centre is the place for you!”
John and Richard beckon, “Welcome, everyone!”
Their enthusiasm is second to none.
In 1856 potash was found,
In Germany, 10,000 ft underground.
The word “potash” John said with a smirk,
Was actually plant ashes spread on the dirt.
First plants were burned, quite a lot.
Then the ashes boiled in a pot.
The plants grew well, tall and fat,
And Potash was born, just like that!
Potassium in the ash made the plants grow.
Potash has 40% KCl, don’t ‘cha know?
In 1943 Radville men drilled for oil,
They had no luck drilling in that soil.
So off to Unity, with a bound,
But potash was still not to be found.
So Unity mined salt, but Esterhazy wanted more.
Germany gave them technology ideas galore.
Late in the ’50’s dedicated men broke ground,
And there it was, potash all around.
To drill out the potash, 3000 ft down or more,
A miner is driven to drill out that ore.
“Keep above the clay and eyeball it for now,”
But today they use a laser (we don’t know how!)
The miner is run on electricity, 4160 volts,
And building the shaft took 17000 bolts.
Through the Blairmore foundation the shaft must go,
But the water-bearing layer is like quicksand. Oh no!
Freezing it is the only way,
We can get that shaft to go down and stay.
Finally, June 8, 1962 it’s done.
What to name it? K1 won!
If underground and lights are flashing,
Four different colours gets everyone dashing.
Mechanics, engineers, electricians and others,
“Call up to dispatch, depending on your colour.”
120 seconds is all that it takes,
For potash to be retrieved from Ice Age lakes.
If potash goes to China, they dye it red,
“It’s the colour of happiness,” they said.
The equipment is huge but it’s no trouble.
They put it together underground on the double.
250 tonnes a miner weighs,
Putting it all together only takes a few days.
K1 and K2 are like one big family,
Hiring more than 1200 employees.
But don’t worry, no need for tears,
K3 and others...who knows 500 more years???
So when travelling down Highway 22,
And wondering what your family should do.
Stop in Esterhazy at the Potash Interpretive Center.
Meet Richard and John, they’ll be your mentors.
© Laurie Johanson and Tara Straker
Day Three, Wednesday August 17th
Potash Mosaic K1 & K2 Mine
and Mill Tour
K1 Underground Mine
The day started out early with a much anticipated trip to
the Esterhazy K1 Potash Mine. After
arriving on site, we were given an orientation and then suited up to go
underground. Our tour guides, Oryan and
Tanner, walked us to the shaft and we waited for our turn. After only a short four and half minute ride
we were almost one kilometer underground.
Once we were underground, we soon learned about the world that exists
that most people have never experienced.
The tunnels, roads and way that things are done was like nothing we had
seen before. After loading into the electric vehicles that are used, we were
off to explore the shop area. We learned
that all machinery and equipment used underground is sent down in pieces and
then assembled for use. The majority of
the larger equipment will never be brought up from underground when the mine is
no longer in production.
While there, Tanner explained how the colour of each person’s hard hat identified something about them. Those wearing green hats had been working at the mine for less than six months. After six months they hand in their green hat to receive a white hat. We saw several people with red hats which signified that they were members of the rescue team and of course all the tourists are given bright orange hats to wear...they definitely saw us coming! After the shop we headed over to a spot where they had just completed the first pass.
After having an opportunity to look more closely at the
miner and ask every question under the sun, we of course needed to have a
little photo op at the very end of the pass.
ORyan and Tanner pointed out the sound that the potash makes after being
mined. It almost sounded like there was
a massive bowl of Rice Krispies that was snapping, crackling and popping! They called these “Potash Fairies.” At this point we looked more closely at the
potash and were given the opportunity to collect a sample or two or ten, no
names mentioned...Trent. We had many
opportunities to ask questions, take a picture or selfie, which seemed to be a
common theme of the trip and explore the area and mining equipment. It was then
time to head back to the shaft and enjoy lunch.
Kendra Waldenberger
Underground Conventional Potash Mine K2 -
We descended 962 m below the surface of the earth to a potash deposit left by a Devonian inland sea. This particular mine, K2 in Esterhazy, is run by The Mosaic Company. One characteristic that makes Esterhazy (and area) unique is that the potash, KCl or potassium chloride, deposits have very little clay or iron making it uniquely whitish in colour. Other places it is quite red. In fact, some iron is added to some of the final products to render it more similar to other products. This speaks to the purity and quality of the product. Saskatchewan is fortunate to be the largest global producer of potash as it is one of the essential minerals for plant growth.
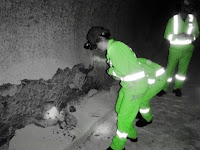
While visiting Esterhazy, I learned a lot of new words, some of which I would like to share with you. OSHA – Stands for Occupational Safety and Health Administration, the American acronym for health and safety. While Mosaic does follow Canadian and Saskatchewan standards, some of the terms carried over from their American parent company. Mosaic is proud that they have not had any incidences of time loss in over a year and any significant incidences in over 60 days. Safety was certainly the overarching theme of our mine visit. It is always the first topic mentioned by Brad from SMA before we leave the bus and it is the last topic we discuss when we leave a site (mostly the relief of taking off the heavy safety boots!). But safety is a serious matter and we have been reminded often that simply walking in a new area can be the most dangerous act. I never once felt slightly unsafe or unsure of what was expected of me in the mine and this is a direct reflection of the mine employees dedication and commitment to their standards.
Back – At first I assumed Jody, the production coordinator and guide extraordinaire, was talking about the tunnels behind us when he mentioned checking ‘the back’ or strengthening ‘the back’. But I soon figured out Jody was talking about the ceiling of the tunnels. The Esterhazy mine has had over 7500 miles of tunnels carved out of the potash bed. To preserve the air quality, non-essential tunnels are closed. The mine still feels like a subterranean city measuring approximately 35 km north to south and 22 km east to west. With a third shaft soon to open (K3) it will be growing even more, although K3 will not be connected with shafts K1 and K2. Ten years ago, Jody was stuck inside a refuge station for 34 hours when there was a fire at K2 (They haven’t had a fire since!). He seemed pretty chill about it. He had a deck of cards, rations and water and he is a mine rescuer himself so he wasn’t too worried – he trusted the safety procedures. He did say that before the fire his wife had never visited the mine, but since then she has visited more than 10 times! Mining can be a hard job even for spouses and families.
Granny – Speaking of families, the term ‘granny’ came up above ground at the mill site. David, an engineer, spoke of loading the granny into the shed. Which does not quite seem kind or gentle. Well, granny means granular, one of the sizes and types of refined potash that Mosaic produces. Depending on its intended use, potash can be crushed, boiled, crystallized and shaken through sieves until is the ideal size for its purpose. Mosaic produces a white crystal powder, standard granular, red standard, crystal granular, granular and raw ore. Other than a bit of bleach for cleaning and vegetable oil for keeping the dust down – this factory only relies on one fresh water source and its own recycled salty brine to make their potash product. The left over NaCl (table salt) makes for an impressive mountain by Saskatchewan standards. Walking on these tailings ponds is apparently quite rough and hard, I assume it is therefore like a glacier. I suggested to David that Mosaic start a salt climbing tourist attraction but he didn’t seem to think this would work well near an active mine. David mentioned that he had low marks in high school math but after completing college, he was able to apply to university and complete an engineering degree. We also met a metallurgical technician who had completed a chemical technician program at Saskatchewan Polytechnic.
Potash – finally, I learned something about the
name of potash. Originally, farmers burn wood, take the ashes and boil them
until a crystal precipitated to the bottom of the pot. This was literally, the
ashes of the pot – potash. And now you know why potassium chloride is commonly
called potash!
Aditi Garg
K2 Mill
The K2 mill is a hot and busy place to be as the potash is
separated into different granular products. There are two processes of
separation, which include brine separation and the other being crystallization.
Each process separates the different final products by size and percent
composition.
The brine separation method is for a larger granular finished
product. By using a brine solution
saturated with potasium chloride to wash the
potash ore, the potash becomes a part of the brine solution. Shakers separate
the larger granular potash to be dried and prepared for sale. The smaller
potash particles within the brine solution are separated by a floatation
method. Detergents are added to the brine/potash solution. The detergents stick
to the potash and air is bubbled into the solution to attach to the coated
potash. The potash floats to the top to be separated by large paddles that skim
off the floating potash. The skimmed potash is dried, sized and prepared for
market. The large granular potash is used primarily for fertilizer but there
are other uses such as a substitute for table salt, sodium chloride.
The process of
separating potash by crystallization is a prepared product with highest percent
composition, 99% pure white potash. The dissolved potash that is within the
brine solution needs to be separated by crystallization due to a concept of
solubility at different temperatures. The solubility of potash is greater at a
high temperature which is different from sodium chloride. Therefore a hot
solution dissolves potash better, the solubility of potash is increased, and
the brine solution becomes supper-saturated. As the super saturated potash
solution cools crystals of potash form first, then it is collected and processed
as a very pure fine grade form of granular potash. This white potash is also
processed through a compactor, which makes this powdery form of crystallized
potash into a larger granular form which is in greater demand by the fertilizer
industry. The compactor is like how one would make a snow ball from snow. Dyes
are added to make the white compacted granular potash red. Even the dust from
any processing of potash is not wasted in the process of making a more
desirable form of granular potash as it is recycled in the mill.
The application of the milling process of potash has direct
connection within Chemistry 30 curriculum included in the outcome of chemical
equilibrium and solubility, CHEM30 EQ2. Solubility curves are used to determine
optimal temperatures for super-saturation and crystallization. Impurities such
as magnesium chloride drastically affect the solubility curve of potassium chloride
and this process of capturing the potash from the ore. The K2 site is favorable
because the ore is primarily made of potash and sodium chloride. The potash ore
with a composition of magnesium is called karnalyte, and is not mined and
brought up to the mill.
Submitted by Jamie
Zaluski
Mosiac K1 Potash Mill at Esterhazy, SK
Instead of a usual blog, I decided to create a mini comic,
starring Potash Pete. Potash Pete, if
you didn’t already know is the mascot of the town of Esterhazy, SK
CAREERS
The days of summer are slowly fading into
cool autumn nights and after a long relaxing break it is hard to imagine a
better career choice than teaching. ...Unless you are a Career consultant and
you are on the hunt to learn as much as possible about mining careers in a
week! Welcome to the whirlwind intro to
careers in Potash/ Coal/ Uranium mining!
A significant portion of Saskatchewan's
industry is attributed to mining, however; very few young people in school are
exposed to the vast number of careers involved to sustain this huge work force.
On the surface one might be aware of the
roles of heavy equipment operators, engineers, and construction tradesmen in
this field but this week we had the chance to "dig a little deeper"
into the subject.
One interesting and reoccurring themes arose
for me at all mine sites ..
The importance of safety!
We were met at each mine site by a rigorous
safety standard and the care and pride in this record was projected proudly.
Every visit began with an introduction to a Safety professional who carefully
instructed us on the obstacles we might face on our visit. We completed
training, forms and even safety talks and various safety cards asking us to
consider the dangers around us in advance. We were suited in properly fitted
PPE and the importance of each item was explained upon orientation. We were
shown the statistics of lost time injury with pride and we were carefully
instructed in the company's safety policy.
I have never had people so concerned about my clumsy nature and tendency
to stumble! This culture of safety is initiated and maintained by all employees
and the Safety professionals employed at a mine site include : Safety managers
, Safety trainers, Safety superintendents, industrial hygienists, OHS workers,
Occupational health nurses, Emergency Response/Mine Rescue teams and the list
continues. Each company boasted their competitive emergency rescue teams awards
in provincial and national annual mine rescue competitions.
Included in this field are the Environmental
engineers and Environmental monitors who ensure safe water, air, and soil
reclamation for the communities surrounding mine sites. This growing
expectation for safe practices even involves engineers who develop and design
equipment for safer work practices and more effective means of ensuring safe
transportation of minerals. The commitment extends to every worker from
reception to trades person and contract workers that enter the building.
The mine safety industry is a booming field
of careers that most young people who imagine mining work as hard hats with
lights on top are never informed of. Training in these professions are offered
as certificate or diploma courses and many of these professionals require
multiple degrees. As a career counsellor my eyes have been opened to the
opportunities that Safety in mining has created!
Donna Nieman
CAREERS
When we look at the careers in the Saskatchewan mining
industry we can see the importance of the natural resources, the process of
extracting this energy from our soil and limiting our carbon footprint with
environmental sustainability regulations.
Each steps provides careers and each mining sector whether
it is uranium, coal, or potash provides
careers in over 100 different jobs within these specialized areas ; Production
Occupations, Trades Occupations, Professional and Physical Science Occupations,
Human Resource and Financial Occupations, Support Workers, Technical
Occupations, and Supervisor , Coordinators, and Foreman’s.
After walking through the different mines this week one can
see the age difference in workers and the opportunity in the near future (2-7
years) for new workers to fill a large portion of positions left by the baby
boomers. These occupations listed above
are visible at each mine. It will depend on the amount of resources in the
ground and world market demands but with continued innovations to technology
the outlook for a career in mining is incredibly strong with any level of
education from grade 12 and up.
The Saskatchewan government goes into great detail about
expansion and opportunity in all industries over the next 5-10 years.
http://publications.gov.sk.ca/documents/310/92066-Industrial%20Employment%20Outlook,%202015-2019.pdf
Tyson Snelling
Day Four, Thursday August 18th
Westmoreland Coal Poplar River Mine
The GeoVenture tour with Westmoreland
Coal Company started with an orientation about the strip mining of coal,
including size of the mine, depth of the coal, quality of coal and future
projections of the coal remaining.

Next we saw the backbone of the operation which is the
dozer. This massive piece of machinery (with wheels that dwarf Willowbunch
Jolly Giant!) is responsible for loading all the coal from the pits. Kendyll
thought the dozer was impressive but was really sham-wowed when she saw the
dragline bucket which we believe is made in #Nantucket. The dragline is responsible for moving
massive amounts of till (loose soft soil) off the top of the coal.
Following that, we toured through the shop seeing all
the different occupations including heavy mechanics, light mechanics and even
an instrumentalist who maintain, update and repair any of the machines on site.
Our second last stop of the day was when we went out
to #6 pit and safely looked at the
operation from the high wall (the border wall over the pit). We saw the
impressive dragline getting ready to start its day of work.
While we were on site, we got a good view of
reclamation projects in their many stages. Reclamation is the act of restoring
the land back to its original state. We saw firsthand how quickly they work to
level and reseed the land so that it can be used for local hay production. We
learned that this operation has the least reclamation time of any type of
mining operation in the province.
We then went into the pit where we saw the dragline in
action. We walked around looking for specific samples of compressed trees which
form the basis for the coal in this area.
This is low grade coal because of the lack of
compression and heat. Although this low grade can’t be used for metallurgy it’s
a cheap and reliable source of energy for our province for decades to come.
Justin Aitken &
Kendyll Kolbeck
Reclamation
Reclamation of the land is an important step in a coal mining operation. Coal mining does not produce waste products or tailings. As a result, the reclamation process is ongoing and almost immediate. Coal mining is done using strip mining. After a section has been excavated, the mined area is filled in using the adjacent cover soil. The land is then revegetated to its natural state. Special care is taken to ensure that rare plants such as Blue Phlox and Least Mouse Tail are preserved by either saving their seeds or transplanting existing plants before the mining process begins. Coal mining has the quickest reclamation process in the mining industry. Within 5-10 years, previously mined land is virtually indistinguishable from nearby unmined land.Reclaimed land is leased to local farmers to be turned into farmland. This land is farmed right away to prevent erosion.
The mine site also partners with Ducks Unlimited to create ponds and wetlands in low lying areas within the mine site.
The reclamation process is finalized when the remaining knolls and cover soil are used to cover the mining roads. In this way, the land is reverted to its original state.
Jackie Preddy
Day Five, August 19th McArthur River Uranium Mine
I always thought of mines as being either open-pit or underground, and of anything within those categories as interchangeable. The potash mines we visited in Esterhazy were hot, dry, deep, and had very low backs (tunnel ceilings). The McArthur River uranium mine was completely different.
The ore at McArthur River is relatively closer to the surface than the potash mines, but is still deep, with working tunnels both (mining takes place between 530 and 640 metres below surface). The rock is harder than potash ore, so it has to be blasted, resulting in the domed tunnels which most people who have never been in a mine picture. Finally, it is wet. The ground and muck is wet and the ground around the ore deposit has to be frozen to prevent flooding and strengthen the rock.Uranium ore is radioactive, but not as radioactive as the fission products produced by nuclear reactors. The uranium deposit at the McArthur River mine is the largest, high-grade uranium mine in the world, with an average grade of over 10% U3O8. The miners are protected by systematic precautions including remote mining techniques so workers are never in direct contact with the ore. A boring bit is pulled up through the ore, from a tunnel (drift) below the ore to a tunnel above, and the ore falls down into the lower tunnel. No one is present in the lower tunnel while this is happening, so no one is exposed to radiation. A remote-controlled loader then picks up the ore, drives to a scanner that analyzes the ore grade and then brings the ore to an underground crushing and grinding circuit where initial processing of the ore starts. The ore is mixed with water to form a slurry which is then pumped 680 m to surface and stored in a slurry tank where it is blended and thickened, removing excess water. The final slurry is then pumped into transport trucks and shipped to Key Lake mill on an 80 kilometer all-weather road.
Visiting
this mine provided practical lessons on the footprint of resource extraction,
barriers to profitability, workplace safety, radiation, chemistry, and career
options, so no matter what you teach, there is useful information waiting for
you on the SMA Geoventure- information which is difficult to find anywhere
else.
They bought us donuts every day, too.
Patrick
Hanley
Day 5, Friday August
19th Key Lake Mill
When we attended the Key Lake Mill we discovered how uranium
was processed in to sellable form. Raw ore from McArthur River is transferred
to Key Lake to isolate U-238. The first process is leaching with sulfuric acid
which makes a complex uranium sulfate that is pulled out of the ore. When the
pH drops below 1 then the uranium is made soluble. Then they precipitate the
other metals by incrementally increasing the pH. As the pH continues to
increase, the uranium ore becomes more
concentrated. The final product is dried to remove leftover aqueous material.
All of these processes relate to the Chemistry 30
Equilibrium and Solubility unit. Students will benefit from real life examples
of precipitation when modeled in the lab.
Darla Down
![]() |
Uranium slurry arriving from McArthur River Mine |
![]() |
Processing to remove uranium |
![]() |
Final product |